All Information from the Shop Floor: Anywhere, Anytime
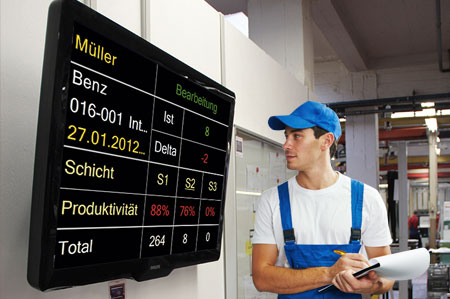
To maintain their overview of the manufacturing in the Shop Floor Management, manufacturing managers and master craftsmen need to have access to both the status of the workstations in real time as well as the historical statistics for machines and processes at any time, from anywhere. This means that the manufacturing managers as well as all of the important information must get out of their offices and onto the shop floor.
Starting Situation before Deploying Cosmino
Many medium-sized manufacturing companies have been implementing the approach of Shop Floor Management over the last few years. The workplaces for manufacturing managers have therefore been moved back into the manufacturing areas. However, critical information required for necessary reactions and decisions is lacking at these locations. Shop floor visualizations are often maintained manually. Regardless of whether the information is up-to-date or not, such an approach is too inflexible to provide the assessments and analyses needed at that point. In addition, a comprehensive view in real time of the status of machines and active orders is also lacking. Subjective decisions and incorrect reactions are the consequence of this lack of information. Introducing an IT system like Cosmino MES Plus supports the employees in the production and is intended to remedy these problems.
Primary Goals of Using Cosmino
1. Correct decisions using standardized key metrics and analyses about each workstation.
2. Actuality of the shop floor visualizations for all workstations and employees.
3. Transparency thanks to access from the shop floor to the entire reporting system, including analyses for the people responsible for manufacturing decisions.
4. Simplified access from the shop floor, including to all active improvement measures.
5. Ability to define measure directly from the shop floor in order to correct misunderstandings in a traceable manner and determine suggestions for improvements immediately and quickly.
6. Standardization and saving time at the periodic continuous improvement process (CIP) meetings directly from the production areas.
7. Complete information about a workstation at that workstation, which includes order information, status of the machine, shift journals, key metrics and active measures.
8. The ability to react quickly based on information if an order does not follow the plan, ensured through comparison of the expected and actual states for each order with the calculation of the remaining duration in real time.
9. A complete overview of all machines with their current status in real time for managers, repairs and even as a mobile option using large screens.
10. Safe processes using automated monitoring of the process parameters compared against the thresholds.
Preparation and Installation of Cosmino
The interface between machines and Cosmino is called MachineConnector and accesses the necessary data directly from the machines’ control systems using an OPC server. Currently, this is the most simple, least expensive way to integrate production machines with Cosmino.
Terminals that already exist and are connected to the machines can be used for the real time visualization of each workstation. Furthermore, all manufacturing areas will be equipped with a central point for information for depicting the key metrics and analyses in digital form.
Cosmino DynaMon covers all of the requirements for reports and key metrics. Individual cockpits have been defined for a variety of hierarchies and areas. All data is acquired from the most granular unit for data acquisition available and accumulated correspondingly for the individual reporting dashboards.
Using Cosmino’s available standard implementations of dialog windows, reports and catalogues of losses leads to an advantageous quick and standardized implementation.
After a pilot phase of several months, the results can be presented to senior management in order to determine the continued rollout process. The rollout can even be performed by the customer’s own plant engineering department, if additional modification are not required.
Achieving the Goals by Using Cosmino
1. Defined key metrics and analyses are always updated and available. They will be the foundation for correct decisions and measurable developments.
2. Creation and distribution of reports is fully automated. A pre-defined selection of key performance indicators is visualized for all employees in an understandable manner using shop floor terminals. From their workstations, employees are also able to access the current figures for their workstations.
3. The web-based software interface provides manufacturing managers with full access to the data, analyses and reports from anywhere.
4. Web browsers make accessing and displaying the reports easy. They can also be operated using touch screens and are intuitive and simple. Measures for improvements can be reviewed from Cosmino ImproveMan using the same interface.
5. Measures, ideas and tasks can be created directly in the system from any Cosmino workstation and will never be lost again. If a connection with the system is not available, a mobile app can be utilized. The app also carries the additional advantage with it that pictures and video clips can be used to support the description of the problem.
6. Cosmino MeetingMan provides support for periodic CIP meetings. Using the prepared meeting template, the software automatically provides all of the reports defined for this purpose for each meeting. The same applies for new improvement ideas and active measures. Tasks set in the meeting appear directly on the responsible party’s To-Do list. Upon conclusion, the minutes of the meeting will be sent to all participants. This makes the team leader’s organizational work easier and reduces effort before and after meetings significantly.
7. Cosmino WorkerPoint supports monitoring the machines. The production employees receive visualizations of the acquired data and all order information. All status changes will are recorded in a journal. Employees also have access to, for example, assessments, measures and instructions for work and testing. Employees can supplement automatically recorded malfunctions on site with root causes. These causes can be analyzed via the reporting system by type, effect, duration and response time and made available to the continuous improvement process.
8. Active comparisons of the expected versus actual states for orders is provided at each workstation using Cosmino WorkerPoint. Among other things, this will make the calculated remaining duration of an order visible, while taking all previous malfunctions into consideration, at all times and in real time.
9. A digital layout of the manufacturing area with all workstations helps visualize the real time status of the machines. Detailed information and access to real time data, shift journals, measures and so on can also be accessed. The digital factory overview can be displayed on a large screen and is also accessible to manufacturing managers and the maintenance team using iPads.
10. If the process parameters are being monitored at the workstation, this information is also accessible by the Cosmino WorkerPoint. Because such values cannot be continuously monitored by operators, Cosmino assumes this task and notifies the responsible employee immediately if any intervention limit has been violated. Automated notification by email or telephone are available in addition to visualization graphs.
Project Summary
Cosmino provides control of the production directly from the shop floor. The employees benefit from the visualizations available at each workstation, since the contexts and effects will be easier to understand. Response time, machine effectiveness and throughput time are key metrics that improve significantly. Employee motivation for increasing effectiveness rises due to the transfer of knowledge.
Better Decisions through Increased Transparency and Knowledge on Site