Why Are Machine Data Not Transferred Directly to ERP and Analysis Tools, but Collected via Acquisition Systems such as PDA or MES?
By Matthias Kohlbrand InCOSMINO AG is turning 35 years old. We would like to take this opportunity to share with you some of the experience we have gained over the years in dealing with production data.
Today, the transfer of data from the machine for production data acquisition software takes place via standardized architectures such as OPC UA, MQTT, REST, etc. The data acquisition system, i.e. PDA, MDA or MES, collects the machine and order data and then makes them available to other systems or own applications. The question arises as to why the data goes the way of acquisition software and is not transferred directly to ERP and analysis applications (e.g. in the Cloud).
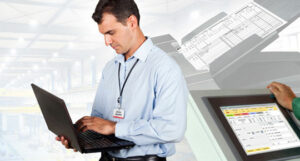
In a few cases, this is certainly possible, but the PLC data, i.e. those of the machine controller, are not sufficient for a consistent data model across all machines. Information not available on the PLC can of course also be added manually via the PDC-specific data entry dialogs. In general, however, machine data can often not be transferred 1:1, but are merely the starting point from which production data acquisition software such as Cosmino then derives the actual situation in production.
Numerous examples can be cited from COSMINO AG projects where the behavior of the PLC signal was not clear at all times. For example, signals that are used to distinguish between processing time and downtime also appeared unexpectedly in deviation from the respective status. Only by constellating several signals could the machine status then be clearly identified.
The behavior of the machine's quantity counters also does not always follow the logic of the actual process; it has happened that they have been zeroed in certain constellations. The PDA must also be able to deal with this, as otherwise there would be minus quantities.
Or there is the case that quantities during a certain plant status (e.g. setup, maintenance, test order) are to be deliberately ignored for the ERP feedback and the evaluations or are to be considered as a separate quantity type. Here, too, the correct booking is made by the PDC, since the machine itself, or its PLC, makes no distinction here.
In another scenario, quantities that fall just outside the booked attendance time of the machine operator have to be dated into this period, otherwise they will be missing for the piecework wage calculation. This is because the employee could, for example, have already logged off for the break or the end of the working day, depending on the point in time during the machining process at which the machine's own quantity counter counts up and the PDA thus supplies the quantity signal.
These were just a few of countless examples. In all these cases, the transferred machine data are evaluated differently or even changed depending on the constellation, as this is the only way they reflect the actual process on the machine.
The fact that this need for "data manipulation" exists at all often only becomes apparent during the project, when the first machine data is taken over and the digital image of the runtime created does not match the expectation. Then it is of immense advantage if our team can directly present a solution based on its wealth of experience.